Photovoltaic Solar Cell Types and Technologies
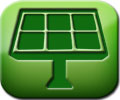
Photovoltaic (PV) cells require only daylight and not direct sunlight in order to generate electricity which means that they can also generate electricity even on cloudy days, but standard types of photovoltaic cells have a very low conversion efficiency. The higher a photovoltaic cells conversion efficiency, the more electricity it generates for a given area of exposure to the sunlight and for standard silicon PV cells this is about 8% increasing to 25% for the more expensive types of photovoltaic cell. This conversion efficiency can be increased to about 40% with the use of concentrating mirrors and lenses. This is because most of the sunlight that arrives at the cells surface passes right through it with little or no effect to the power output.
Also excess photon energy that is not converted into electricity is wasted as heat. The heating effect of the silicon cell results in the maximum efficiency of a silicon PV solar cell in hot sunlight being very low. Then one of the primary factors in selecting a given semiconductor material for use as a photovoltaic material is its maximum conversion efficiency and power output. The average power output from a standard silicon photovoltaic cell is also dependent on the application, the suns irradiance on the photovoltaic cell and the size of the actual cell.
Types of Silicon Used in Photovoltaics
There are different types of photovoltaic cells available to buy, but mainly they are manufactured from silicon (Si), the second most abundant element in the Earth’s crust (after oxygen), and which is the same material from which sand is made. Silicon on its own is not very pure and must therefore be refined to produce a purity of up to 99.99% pure before it can be used as a semiconductor material in many different types of photovoltaic cells, transistors or digital IC’s. The use of silicon in the manufacture of photovoltaic cells produces the stereo typical uniform blue coloured PV cell which we see on roof tops and the sides of buildings.
The two major types of photovoltaic cell materials used are crystalline silicon and thin film deposits, which vary from each other in terms of light absorption efficiency, energy conversion efficiency, manufacturing technology and cost of production. Crystalline silicon PV cells are the most common type of photovoltaic cell in use today and are also one of the earliest successful PV devices.
The three general types of photovoltaic cells made from silicon are:
- Mono-crystalline Silicon – also known as single-crystal silicon
- Poly-crystalline Silicon – also known as multi-crystal silicon
- Thin Film Silicon
Crystalline Silicon (c-Si)
This is the most common technology used to produce photovoltaic cells representing about 90% of the market today. Crystalline photovoltaic cells are made from silicon which is first melted, and then crystallised into ingots or casting’s of pure silicon. Thin slices of silicon called wafers, are cut from a single crystal of silicon (Mono-crystalline) or from a block of silicon crystals (Poly-crystalline) to make individual cells. The conversion efficiency for these types of photovoltaic cell ranges between 10% and 20%.
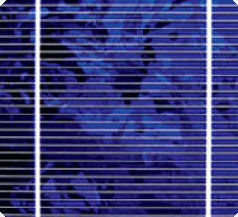
Poly-Crystalline Silicon
- Mono-crystalline Silicon is a type of photovoltaic cell material manufactured from a single-crystal silicon structure which is uniform in shape because the entire structure is grown from the same crystal. High purity silicon is melted in a crucible.A single-crystal silicon seed is dipped into this molten silicon and is slowly pulled out from the liquid producing a single-crystal ingot. The ingot is then cut into very thin wafers or slices which are then polished, doped, coated, interconnected and assembled into modules and arrays. These types of photovoltaic cells are also widely used in photovoltaic panel construction.Compared to non-crystalline cells, the uniform molecular structure of the silicon wafer makes it ideal for transferring loose electrons through the material resulting in a high energy conversion efficiency. The conversion efficiency for a mono-crystalline cell ranges between 15 to 20%.Not only are they energy efficient, mono-crystalline photovoltaic cells are highly reliable for outdoor power applications due to their wafer thickness. However, to make an effective PV cell, the silicon has to be “doped” with other elements to make the required N-type and P-type conductive layers.
- Poly-crystalline Silicon also known as multi-crystalline silicon, is cast to produce a silicon ingot. The silicon molecular structure consists of several smaller groups or grains of crystals, which introduce boundaries between them. Poly-crystalline PV cells are less energy efficient than the previous mono-crystalline silicon PV cells because these boundaries restrict the flow of electrons through it by encouraging the negative electrons to recombine with the positive holes reducing the power output of the cell. The result of this means that a poly-crystalline PV cell only has an energy conversion efficiency of between 10 to 14%. However, these types of photovoltaic cell are much less expensive to produce than the equivalent single mono-crystalline silicon due to their lower manufacturing costs.
Thin Film Solar Cell
Thin Film Solar Cells are another type of photovoltaic cell which were originally developed for space applications with a better power-to-size and weight ratio compared to the previous crystalline silicon devices. Thin film photovoltaics are produced by printing or spraying a thin semiconductor layer of PV material onto a glass, metal or plastic foil substrate. By applying these materials in thin layers, the overall thickness of each photovoltaic cell is substantially smaller than an equivalent cut crystalline cell, hence the name “thin film”. As the PV materials used in these types of photovoltaic cells are sprayed directly onto a glass or metal substrate, the manufacturing process is therefore faster are cheaper making thin film PV technology more viable for use in a home solar system as their payback time is shorter.
However, although thin film materials have higher light absorption than equivalent crystalline materials, thin film PV cells suffer from poor cell conversion efficiency due to their non-single crystal structure, requiring larger sized cells. Semiconductor materials used for the thin film types of photovoltaic cell include: Cadmium Telluride, Amorphous Silicon and Copper Indium diSelenide or CIS.
- Cadmium Telluride, (CdTe) is a poly-crystalline semiconductor material made from cadmium and tellurium. Thin film cadmium telluride has a high light absorption level so the amount of CdTe required can be quite minimal with less than 1.0 microns of semiconductor material is needed to effectively absorb sunlight for the solar device to perform.
Thin Film CellAlthough the process of spraying or printing the thin film is relatively easy making it cheap to manufacture these types of photovoltaic cell, the main material, cadmium is a toxic heavy metal can pollute the environment if the cell is damaged or broken. Another disadvantage of these types of photovoltaic cells is that the conversion efficiency for a cadmium telluride PV cell can be low at less than 10%. - Amorphous Silicon, (a-Si) is a non-crystalline form of silicon that is widely used in calculators, consumer electronics and solar garden products that require a small current at a low voltage. Of the different types of photovoltaic cell available, amorphous silicon has the highest light absorption of over 40 times higher than crystalline silicon. The advantage of this is that a much thinner layer of amorphous silicon material is required to make a thin film PV cell reducing manufacturing costs and price.
- Amorphous silicon cells have various advantages and disadvantages. On the plus side, amorphous silicon can be deposited on a variety of low cost rigid and flexible substrates such as polymers, thin metals and plastics as well as tinted glass for building integration. However, on the minus side, two of the main disadvantages of amorphous silicon (a-Si) is its very low conversion efficiency ranging from between 7 to 9% when new, degrading down within a few months of exposure to sunlight to less than 5%.
- Copper Indium diSelenide, (CIS) is another type of poly-crystalline semiconductor material composed of Copper, Indiumand Selenium, (CuInSe2). Thin film CIS types of photovoltaic cell can produce conversion efficiencies of nearly 10%, almost double that of amorphous silicon without suffering from the same outdoor degradation problems due to their thicker film. Also CIS cells are one of the most light-absorbent semiconductor compounds absorbing up to 90% of the solar spectrum.
- Although Copper Indium diSelenide, CIS cells are efficient, the complexity of the formulation of the semiconductor compound makes them difficult to manufacture and expensive. Also, Indium is a relatively expensive material due to its limited availability with manufacturing safety issues a concern as hydrogen selenide is an extremely toxic gas.
- Copper Indium Gallium diSelenide, (CIGS) is another type of photovoltaic cell. It is basically a P-type poly-crystalline thin film material based on the previous copper indium diselenide (CIS) semiconductor material. The addition of small amounts of the compound Gallium (Ga) produces a photovoltaic cell with a higher conversion efficiency of around 12% from the same amount of sunlight with an open circuit voltage of about 0.7 volts. This is because Gallium, which is a liquid similar to mercury at room temperatures, increases the light-absorbing band gap of the cell, which matches more closely the solar spectrum, thereby improving its conductivity allowing electrons to freely move through the cell to the electrodes.
Other Types of Photovoltaic Cell
As well as the commonly used types of photovoltaic cell mentioned above, and which account for about 95% of the commercial market, other types of photovoltaic cell currently being developed include:
- Multijunction PV Cells – These are types of photovoltaic cell designed to maximise the overall conversion efficiency of the cell by creating a multi-layered design in which two or more PV junctions are layered one on top of the other. The cell is made up of various semiconductor materials in thin-film form for each individual layer.
The advantage of this is that each layer extracts energy from each photon from a particular portion of the light spectrum that is bombarding the cell. This layering of the PV materials increases the overall efficiency and reduces the degradation in efficiency that occurs with standard amorphous silicon cells. - Dye-Sensitive PV Cells – This type of technology is considered to be the 3rd generation of solar cells. Instead of using solid-state PN-junction technology to convert photon energy into electrical energy, an electrolyte, liquid, gel or solid is used to produce a photo-electrochemical PV cell. These types of photovoltaic cells are manufactured using microscopic molecules of photosensitive dye on a nano-crystalline or polymer film.
The photon light energy being absorbed by the dye releases electrons into the conduction band causing a flow of the electricity through the semiconductor. The advantage of a dye-sensitive nano-crystalline photo-electrochemical photovoltaic cell is that the dye can be screen printed onto any surface producing conversion efficiencies of around 10%. - 3D Photovoltaic Cells – This type of photovoltaic cell uses a unique three-dimensional structure to absorb the photon light energy from all directions and not just from the top as in convectional flat PV cells. The cell uses a 3D array of miniature molecular structures which capture as much sunlight as possible boosting its efficiency and voltage output while reducing its size, weight and complexity.
Photovoltaic Cell Conclusion
Photovoltaic (PV) cells create electricity from sunlight by converting photons into electrons without creating any environmental problems such as pollution and waste. Photovoltaic (PV) cells are made of special materials called semiconductors such as silicon (Si), which is currently the most commonly used. Crystalline silicon has been the workhorse of the PV cells for the past two decades and in fact, over 95% of the solar cells produced worldwide are composed of crystalline silicon. However, recent developments in solar cell technologies have produced thin-film and other types of photovoltaic cells with greater conversion efficiencies.
There are many different “types of photovoltaic cell” available on the market, but an individual photovoltaic cell produces up to about 2 watts of power, which may be sufficient to power a calculator or a wrist watch, but to generate any meaningful solar power that we can use as an alternative power source, individual solar cells need to be combined together to produce modules, panels or large solar arrays and this is discussed further in the next tutorial.
In the next tutorial about “Solar Power”, we will look at how we can connect together these individual photovoltaic cells to produce a larger Solar Photovoltaic Panel to produce higher voltages and currents.
http://www.alternative-energy-tutorials.com/solar-power/photovoltaic-types.html
ليست هناك تعليقات:
إرسال تعليق